Coût total : 34,38 €
Temps de réalisation : 2h15
Afin de ne pas alourdir mon article sur la centrifugeuse, j’ai préféré écrire un article à part concernant sa fabrication.
En effet, contrairement aux autres objets que je propose, celui-ci demande un peu plus d’attention et de matériel même si l’ensemble reste simple et à porter de tout le monde.
Matériel spécifique :
- une découpeuse laser. Au collège, dans la salle technologie ? Dans un FabLab à proximité ? Á titre personnel, je vais à Béthune à La Fabrique. Ils sont super sympa, disponible, de bon conseils, et avec des tarifs très abordables.
- une imprimante 3D. En technologie c’est devenu banal et là encore un fablab à proximité vous rendra grand service. Enfin, les prix deviennent tellement intéressant qu’un achat est envisageable. Pour plus d’infos, je vous conseille les tests d’Heliox sur Youtube.
De mon côté, j’ai une MicroDelta : rapide, de fabrication française (important pour moi), un service après-vente de qualité, de forme originale et peu encombrante mais une surface d’impression réduite en comparaison avec les plateaux classiques.
- un fer à souder et le matériel associé. Les prix sont hyper abordables pour ce genre de matériel.
Liste des matériaux et coût :
Les prix indiqués proviennent de magasin de bricolage très connu et de mon site préféré 😉 pour l’électronique : gotronic.fr
Si vous trouvez moins cher, merci de me l’indiquer soit dans les commentaires, soit en me contactant.
Matériau | Quantité | Prix unitaire (euros) | Total (euros) |
---|---|---|---|
MDF 6mm | 1 265,44 cm2 | 20 € les 30 500 cm2 | 0,83 |
Plaque transparente 3 mm | 295,84 cm2 | 10,9 € les 5000 cm2 | 0,65 |
Aluminium pour charnière (0,6cm de diamètre) | 4 cm | 1 m pour 3,60€ | 0,15 |
Découpe laser | 10 minutes environ | 3 € les 5 minutes | 6,00 |
Vis / écrou | 3 | 30 pour 3,45 € | 1,04 |
Plastique pour impression 3D | 25g | 20,99 € pour 1000g | 0,53 |
Tubes à essais | 2 | 50 pour 13, 99€ | 0,56 |
Alimentation 9V | 1 | 8,60 | 8,60 |
Embase alimentation | 1 | 1,60 | 1,60 |
Moteur 6-12V | 1 | 3,10 | 3,10 |
Pignon pour moteur | 1 | 0,20 | 0,20 |
Plaque d’essai | 9×5 cm | 10x20cm pour 4,60€ | 1,04 |
DEL verte | 1 | 10 pour 0,7 € | 0,07 |
Clips pour DEL | 1 | 0,08 | 0,08 |
Interrupteur | 1 | 0,90 | 0,90 |
Réflecteur optique | 1 | 2,50 | 2,50 |
Microrupteur | 1 | 1,50 | 1,50 |
Douille à cosse | 1 noire et 1 rouge | 1,60 | 3,20 |
Cosse | 2 | 10 pour 0,80 € | 0,16 |
Résistances 220, 470 et 10k | 3 | 10 pour 0,20 € | 0,06 |
Diode 1N4007 | 1 | 0,08 | 0,08 |
Condensateur (47nF) | 1 | 0,15 | 0,15 |
Contacts NDR | 12 | 25 pour 0,75 | 0,33 |
Connecteur long | 2 x 6 | 1 lot | 0,70 |
Boitier NSR | 6 | 25 pour 0,80 € | 0,20 |
Fils | ~1 m | 10 m pour 1,5€ | 0,15 |
Le total est de 34,38 euros.
C’est environ 8 à 10 fois moins cher qu’une petite centrifugeuse et celle-ci permet de mesurer la vitesse de rotation quand les autres ne font qu’afficher, parfois, cette valeur. C’est donc plus intéressant pédagogiquement.
On peut « grappiller » quelques euros avec un capteur optique moins cher, avec des douilles plus simples, sans les contact NDR, …
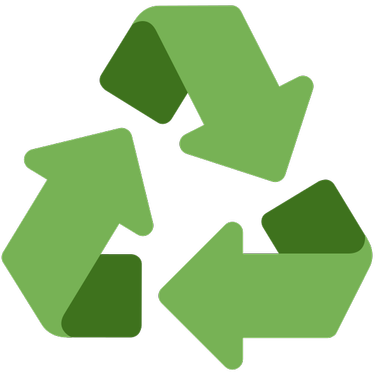
Avec de la récupération, on peut vraiment faire des économies. Il doit bien avoir une veille alimentation qui traine chez soi, au laboratoire, des DELs, des interrupteurs, …
J’ai voulu cette centrifugeuse facilement réparable. Les contacts NDR permettent un dépannage rapide et facile. Pas besoin de dessouder et de tout démonter. En revanche, le temps de montage sera plus long .
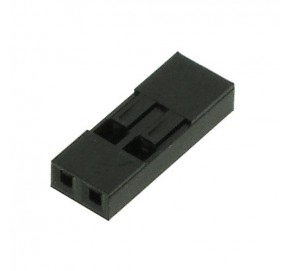
La fabrication
Imprimer en 3D
5 minutes
pour lancer l’impression
Dans un FabLab, en salle de technologie, un achat impulsif ;-), démarrer l’impression en 3D. Elle dure environ 1H30, c’est selon la machine utilisée.
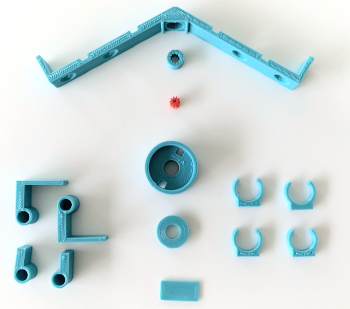
J’ai imprimé en couche de 0.2 mm avec du PLA. La qualité est meilleure avec cette épaisseur de couche mais le travail prend plus de temps. Mais comme pendant l’impression, je fais la découpe, l’assemblage, les soudures, … ainsi la durée m’importe moins.
En bas à gauche de l’image, les pièces pour la charnière du couvercle transparent doivent être imprimées en « miroir ». C’est pour cela que dans le dossier à télécharger, il y a seulement 2 fichiers « charnières »
Pour les « arches » permettant le maintien du tube. Il y a aussi seulement 2 fichiers. Un pour le maintien en haut et un pour le bas. Le tube est plus fin vers le bas. Comme il y a 2 tubes, il faut l’imprimer 2 fois … dingue non ? 😉
Le pignon rouge n’est pas à imprimer. Il est a acheté.
Préparer le support des tubes
10 minutes
Un ébavurage est nécessaire au niveau des trous sur le support du tube et aussi pour la partie qui va accueillir le pignon. Une petite lime ou encore mieux une Dremel fera l’affaire.
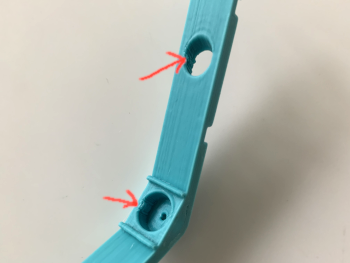
Selon la qualité d’impression un petit coup de lime sera peut être nécessaire pour insérer le pignon dans son support. Parfois, j’utilise une pince pour légèrement forcer l’insertion.
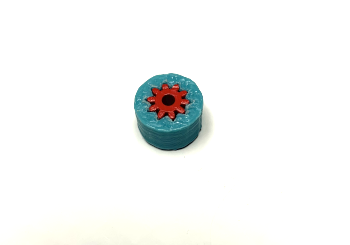
Pour finir, le pignon bien inséré dans son emplacement se place au centre du support de tubes (flèche rouge du bas sur l’image précédente) avec une pointe de colle de type « Super Glue ».
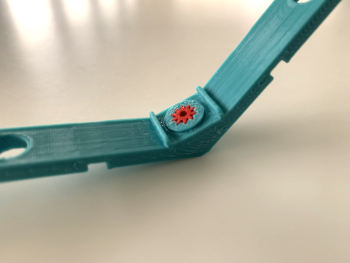
Enfin, il ne reste plus qu’à coller les arches sur leur emplacement respectif, avec les plus larges vers le haut :
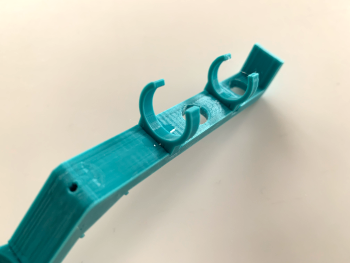
Découper le MDF 6mm
5 minutes de préparation des fichiers
10 minutes de découpe
J’ai acheté une plaque de 80 x 60 cm que j’ai découpé en deux pour qu’elle rentre dans la découpeuse laser.
J’utilise le logiciel RDWorksV8 qui est libre et gratuit et c’est celui utilisé pour la découpeuse laser. Je peux ainsi préparer le fichier chez moi. Un petit tour au FabLab et la découpe commence :
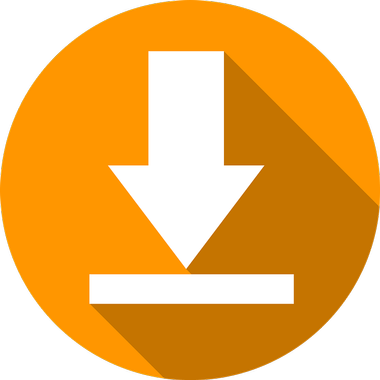
Attention ce fichier n’est valable que pour une épaisseur de 6 mm :
Télécharger le fichier pour la découpe laser.
Le diamètre du rayon laser est réglé à 0,15 mm. Tout est de la découpe sauf pour l’inscription « Centrifugeuse » où là il faut effectuer un « Scan ». Une gravure est prévue pour marquer l’emplacement du moteur et le chemin des fils.
Le fichier ne contient pas la découpe pour le couvercle en plastique transparent car c’est ultra simple : c’est un carré de 172 x 172 mm. Dans le logiciel, c’est réalisé en 2 clics.
Assembler les découpes
15 minutes
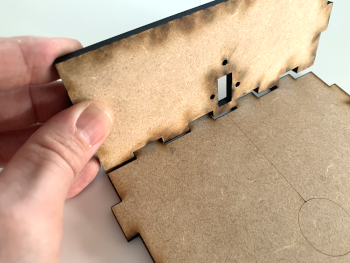
Le réglage de la découpe fait que les pièces s’emboitent parfaitement ou force légèrement. Un rapide coup de lime est alors parfois nécessaire sur les encoches.
Pour être sûr du maintien, j’ajoute un point de colle de type « Super Glue » au niveau des encoches.
La découpe laser engendre des fumées qui « tâchent » le matériau (à droite sur la photo). J’aime bien cet effet sur le dessus (à gauche sur la photo au niveau des encoches). En revanche, en dessous, c’est plus « moche ». Donc lors de l’assemblage je fais en sorte que le côté moins joli ne se voit pas. (A l’intérieur de la boite, par exemple.
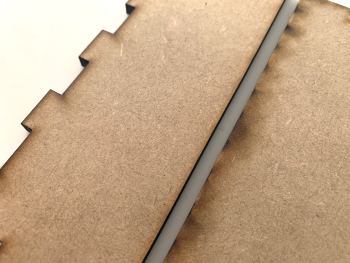
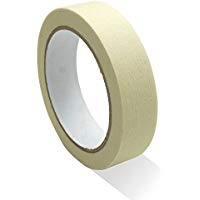
Sinon, on peut utiliser du ruban de peinture. On couvre la plaque MDF des deux côtés de ce scotch et ensuite on effectue la découpe. Il ne reste plus qu’à l’enlever. Les fumées sont restées sur le ruban et non sur le MDF.
C’est plus long à préparer et plus cher… c’est selon l’aspect que l’on souhaite obtenir.
Attention à bien positionner certaines découpes :
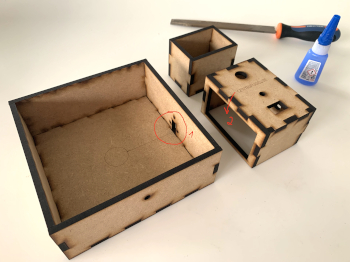
- L’orifice du capteur optique doit être dans le prolongement de la gravure du chemin des fils (1).
- La découpe rectangulaire du panneau de commande doit être placé à gauche (2).
Ne pas coller les 3 blocs ensemble pour le moment. L’emplacement de l’électronique en sera facilité.
Préparer la plaque d’essai à bandes
5 minutes
Tracer sur une plaque d’essais un rectangle aux dimensions de 9 cm sur 5 cm. Le tracé tombe sur les perçages (ou presque). Attention aux sens des bandes cuivrées, elles sont parallèles aux petits côtés :
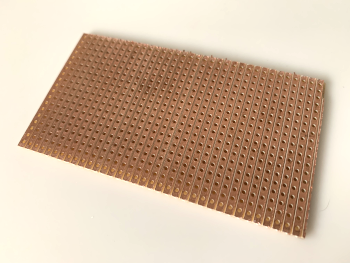
Avec un cutter et une règle, passer plusieurs fois de chaque côté de la plaque et en appuyant assez fort. Il suffit ensuite de la plier en la maintenant fermement de chaque coté du tracé. Elle cède alors très facilement et sans bavure.
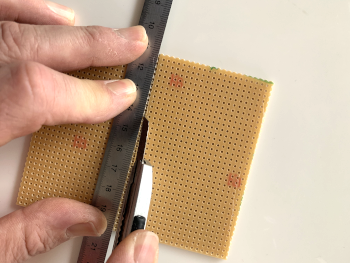
Avec une lime, ajuster aux bonnes dimensions :
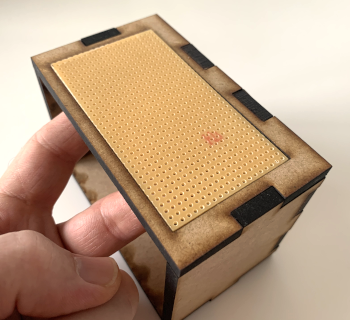
Percer et découper la plaque à l’aide du patron et d’une petite perceuse
10 minutes
Un foret de 3,2 mm fait l’affaire. N’hésiter pas à agrandir un peu les trous pour faciliter l’assemblage futur.
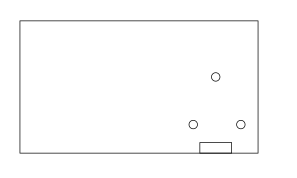
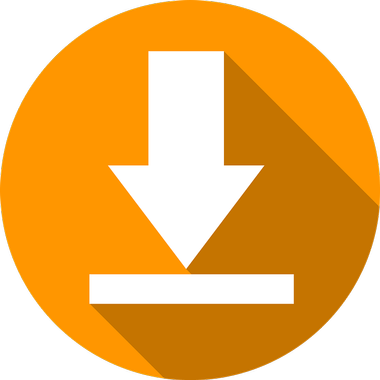
Télécharger le patron en svg.
L’ouvrir avec le logiciel gratuit Inkscape
Imprimer sur du bristol, c’est plus rigide.
Vérifier le perçage et la découpe pour le passage des fils :
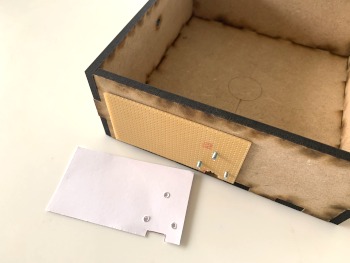
Séparer les 3 pistes comme sur la photo avec un cutter ou une Dremel. Pour l’emplacement précis, vous pouvez vous aider de l’image ci-dessous ou de l’image schématique du montage électronique (voir plus bas).
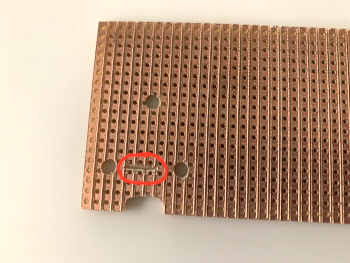
Souder les composants
30 minutes
Le schéma électrique :
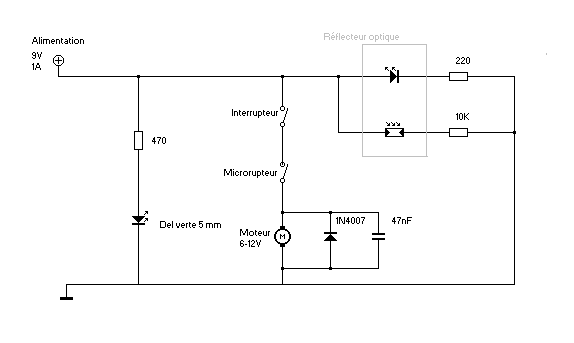
L’emplacement réel sur la plaque. Les bandes cuivrées sont derrière.
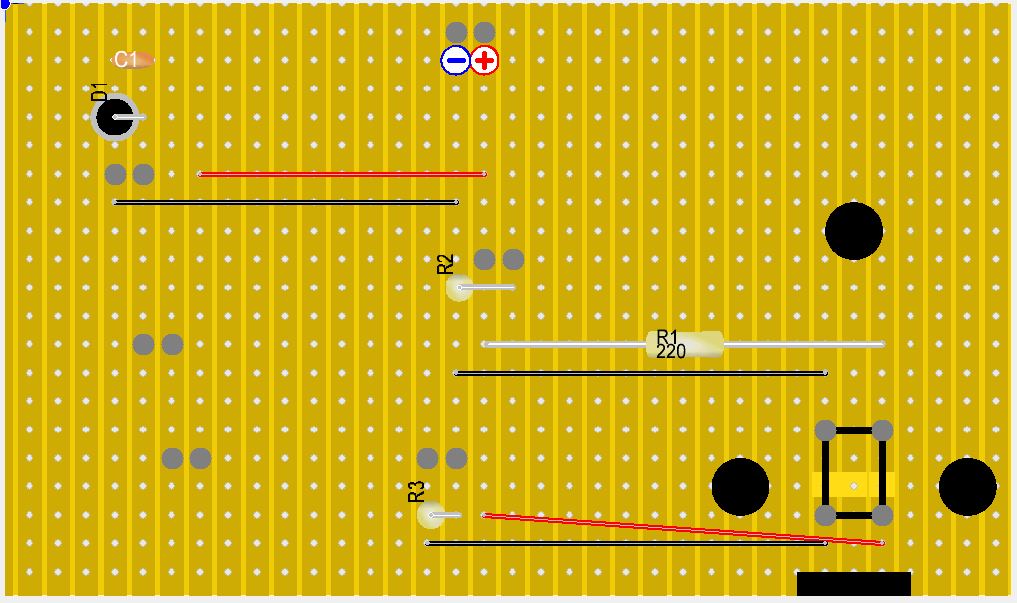
C’est, bien sûr, adaptable à vos besoins, envie…J’ai essayé de faire en sorte qu’il y ait un minium de « grattage » de cuivre. Les deux points gris côte à côte correspondent au connecteur long. Le cadre noir représente le réflecteur optique qui sera à souder « à l’envers ».
On obtient :
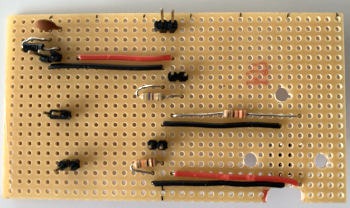
Penser à passer un petit coup de cutter entre les pistes. Un microcontact peut se faire sans s’en apercevoir :
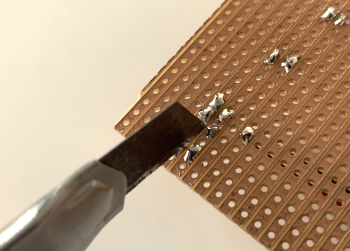
Enfin, souder de l’autre côté le réflecteur. Le bord supérieur doit être à environ 1,5 cm de la plaque :
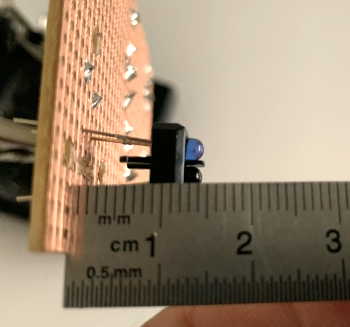
Préparer les fils
15 minutes
Les connecteurs sont bien sûr facultatif. C’est un léger surcoût certes mais ils permettent un dépannage vraiment facile par la suite et surtout un montage bien plus aisé. Avec une petite pince, c’est assez rapide. Ou encore plus simple avec une pince dédiée.
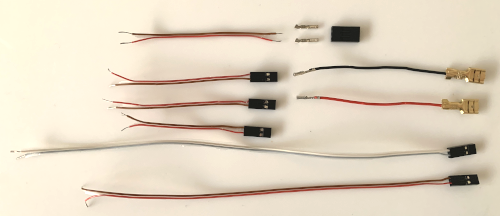
J’utilise des nappes de fil. On peut ainsi séparer le nombre de fils que l’on souhaite et ils restent solidaires. Pour les fiches bananes, j’utilise des fils un peu plus gros car les cosses sont plus grandes. Une longueur de 8 cm de fils suffit pour l’interrupteur, la DEL, les fiches bananes et l’embase. 23 cm pour le microrupteur et 22 cm pour le moteur.
Étamer les fils et souder les composants
10 minutes
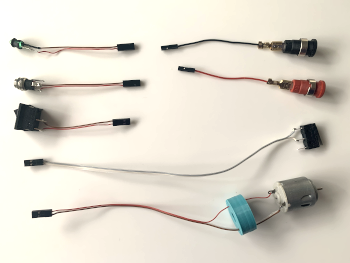
J’ai mis une gaine rétractable sur l’anode de la DEL afin d’éviter un faux contact. Penser à faire passer les fils dans le support du moteur avant la soudure. Le moteur force un peu quand on l’insère dans son support. C’est normal c’est pour le bloquer. Vérifier qu’il n’y a pas de « bavures » dues à l’impression 3D. Si c’est le cas, limer un peu et finaliser avec une pince en forçant légèrement.
Attention aux polarités pour l’embase de l’alimentation. Le fil rouge correspond à la borne positive de l’alimentation.
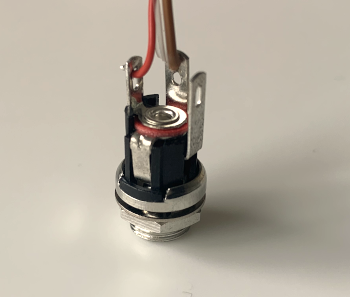
Coller les blocs ensemble
2 minutes
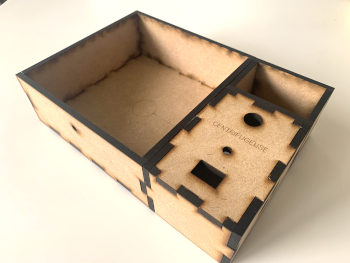
Placer les vis
1 minute
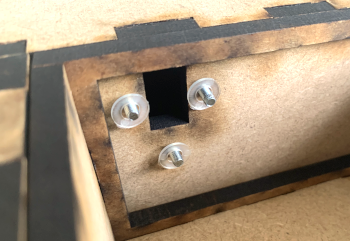
J’ai mis des rondelles en plastiques pour surélever la plaque et éviter le contact entre les vis et les bandes cuivrées.
Solidariser la plaque électronique avec les écrous :
2 minutes
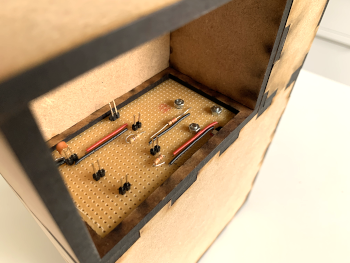
Coller le support de l’embase
1 minute
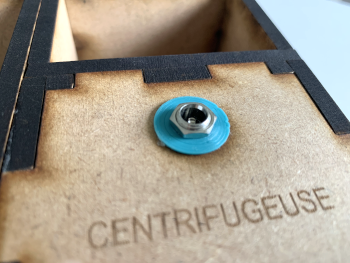
Deux ou trois points de colle suffisent. Visser ensuite l’embase.
Connecter les composants sur la plaque électronique
2 minutes
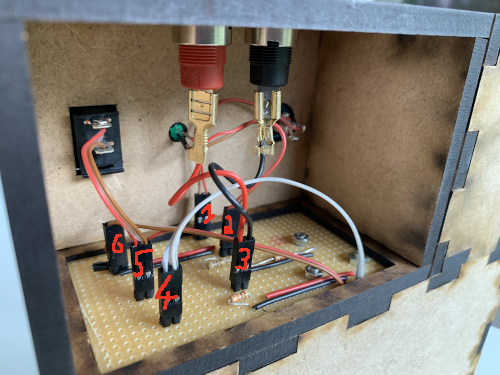
Insérer l’interrupteur et la DEL puis fixer les fiches bananes et enfin connecter les fils à la plaque. Tous les fils rouge correspondent à l’orientation vers la borne positive de l’alimentation.
- L’embase. Attention à la polarité.
- La DEL. Attention à la polarité.
- La tension du capteur. Attention à la polarité.
- Le Microrupteur.
- L’interrupteur
- Le moteur
Coller le moteur bien au centre
1 minute
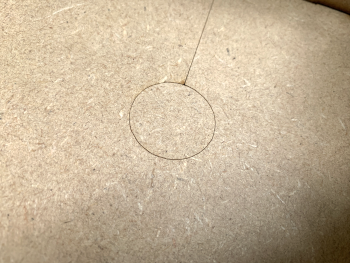
La gravure permet de bien centrer le moteur avec son support. Le trait permet aussi de placer la colle puis d’appliquer les fils.
Coller le microrupteur
1 minute
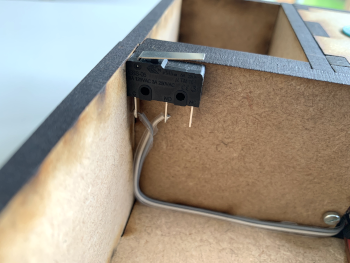
Faire affleurer le haut du microrupteur aux bordures supérieure du MDF. Coller les fils dans les angles.
Découper des bouts de tige d’aluminium et les emboiter dans les supports
5 minutes
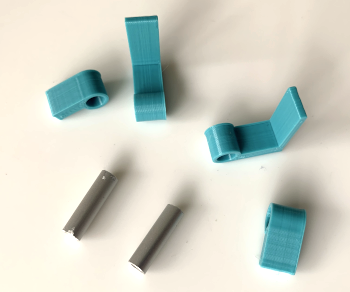
Les tubes font 6 mm de diamètre. Une longueur de 2 cm convient parfaitement. Limer les extrémités puis emboiter les pour vérifier que la rotation des embouts est aisée.
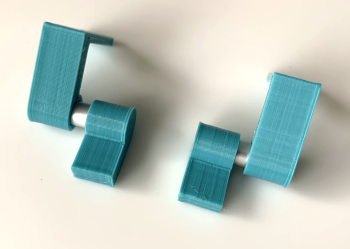
La surface de contact doit être bien lisse et plate pour les supports. N’hésiter pas à les poncer. C’est important sinon même avec une colle forte ils ne colleront pas.
Coller la charnière
1 minute
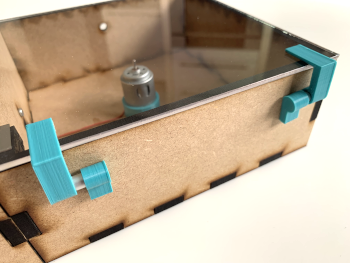
Mettre un point de colle sur les supports touchant le MDF. Bien positionner l’ensemble et attendre que la colle prenne.
Faire de même avec le couvercle.
Coller le support pour le couvercle
1 minute
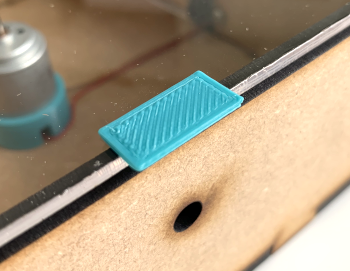
Il permet d’ouvrir le couvercle facilement.
Placer le support des tubes
1 minute
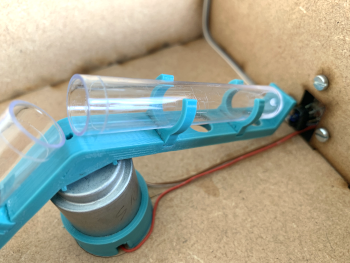
Forcer l’insertion du support dans l’axe du moteur. Vérifier qu’il ne touche pas le capteur.
La centrifugeuse est prête !
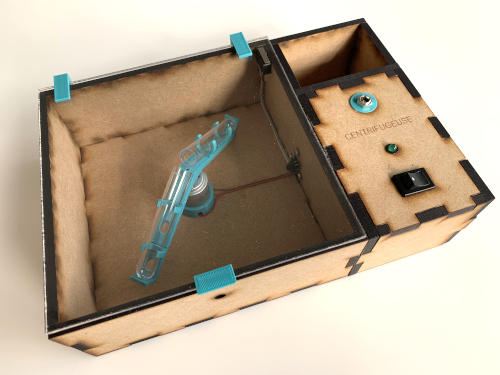
Brancher l’alimentation et faire un test de fonctionnement.
Fabrication du module pour l’Arduino
L’oscilloscope n’est plus d’actualité au collège et son prix n’est pas du tout accessible pour les budgets de l’établissement. Pourtant, la fréquence doit être abordée. Pourquoi ne pas calculer le nombre de tours par seconde de la centrifugeuse ? On peut aussi chercher la vitesse tangentielle des tubes, non ? Je vous propose ici un montage permettant de réaliser les deux.
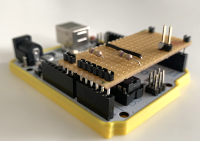
Le module pour l ‘Arduino est ultra-simple à fabriquer !
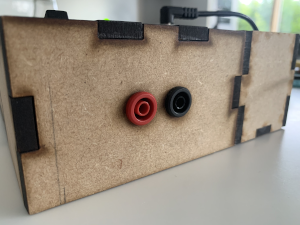
Les fiches bananes sont branchées sur la centrifugeuse
On mesure, alors, la tension du capteur optique en fonction du temps.
Agrandissez la vidéo pour voir les détails !
Combien ça coute ?
Concernant le matériel, j’ai choisi parmi les moins chers, il me semble. Là encore si vous trouvez moins cher, laisser un commentaire ou contactez-moi.
La carte Arduino que propose Gotronic est quasiment 2 fois moins cher que la carte “officiel”. Je l’ai testé maintes fois et je n’ai eu aucun souci. C’est donc celle-là que je propose. Le seul inconvénient : le câble fourni est un peu court. Si vous en avez qui trainent (USB A – USB B) gardez-les !
Matériau | Quantité | Prix unitaire (euros) | Total (euros) |
---|---|---|---|
Une carte Arduino | 1 | 10,90 | 10,90 |
Plaque d’essai | 2,5 cm x 5,3 cm | 10x20cm pour 4,60€ | 0,30 |
Connecteur long | 12 | 40 pour 0,70 euros | 0,20 |
Résistances | 2 | 10 pour 0,20 € | 0,04 |
Fil | 2 cm | 0,25 € pour 1m | 0,01 |
Le cout total est de 11,45 euros.
Le prix est dérisoire face à un oscilloscope ou du matériel Exao. Évidemment la qualité s’en ressent ! Mais franchement, c’est acceptable et largement suffisant pour le collège, je trouve.
Le circuit électronique du module
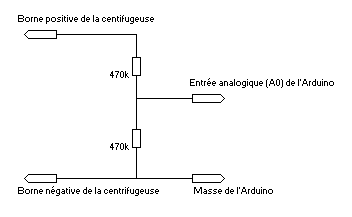
Utra-simple, je disais !
Implantation des composants :
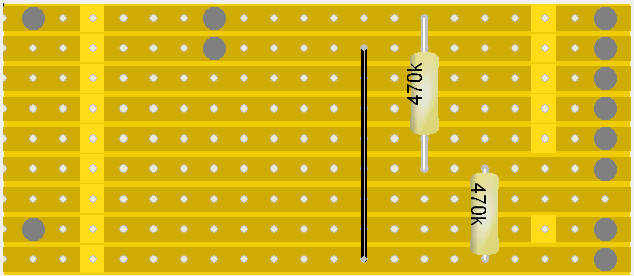
Bien enlever le cuivre aux bons endroits !
Les disques gris correspondent auxconnecteurs
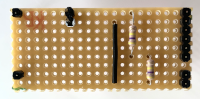
Voilà le résultat.
Un coup de blanc pour ne pas se tromper dans l’orientation des fils
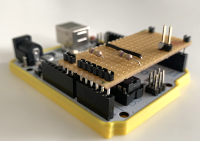
Placer le module sur l’Arduino.
Ne pas se tromper de sens ! 😉
Pour éviter à la carte de toucher la surface de la table, un petit support à imprimer en 3D est bien utile. Vous pouvez en trouver sur thingiverse.
Parfois, il est un peu large. Je chauffe légèrement les bords avec un briquet et j’aplatis les angles.
La partie informatique
Brancher l’Arduino à un port USB de l’ordinateur. Une Del verte doit éclairer.
Configurer la carte Arduino :
- Télécharger l’IDE de la carte Arduino et l’installer. (Choisir Arduino IDE et non le WEB Editor.)
- Télécharger le programme suivant que j’ai conçu, l’ouvrir en double-cliquant dessus et téléverser le programme dans l’Arduino.
Si vous n’êtes pas habitué à l’IDE de l’Arduino, voici la procédure :
- Dans OUTIL, choisir comme type de carte “Arduino/Genuino…” et le port COMX (ici c’est le port COM3, mais le chiffre peut différer)
- Cliquer sur TELEVERSER . Des messages dans la zone noir, en bas, vont s’afficher.
- Dans la zone 3, si tout se passe bien, vous devriez voir écrit : “Téléchargement terminé”.
Le plus dur est fait et n’est à faire qu’une seule fois. Le programme est maintenant présent “dans” l’Arduino. Laisser là brancher.
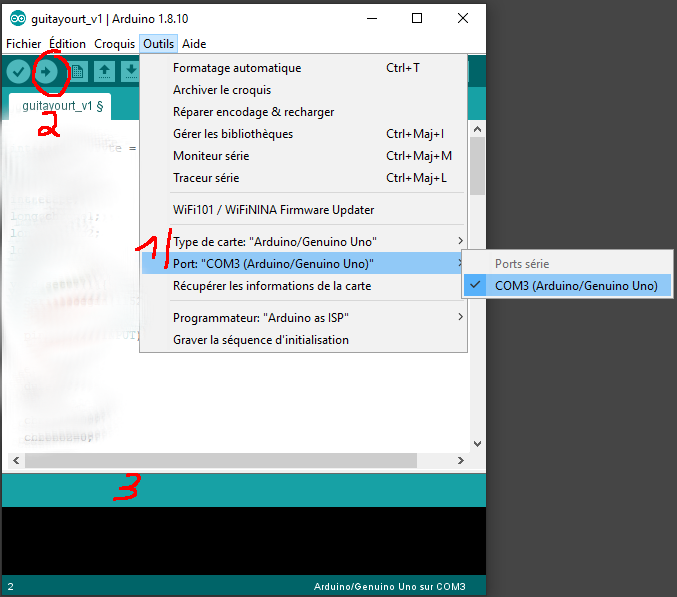
2 possibilités : interface web ou programme autonome
1 – Interface web :
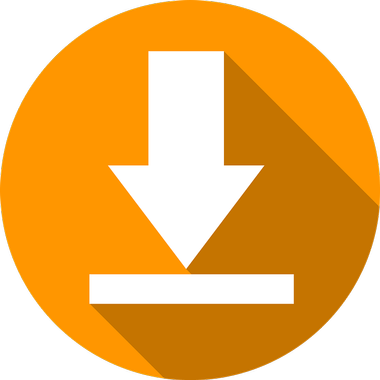
Télécharger le logiciel qui fait l’interface entre l’Arduino et la page WEB qu’il faudra ouvrir par la suite.
Merci aux concepteurs de ce logiciel !
- Dézipper le dossier
- Exécuter le fichier p5.serialcontrol.exe
- Vérifier qu’un port COM est présent (voir photo, le chiffre peut varier) et UN SEUL ! Sinon débrancher les autres appareils.
- Vous pouvez réduire le programme et surtout ne pas le fermer.
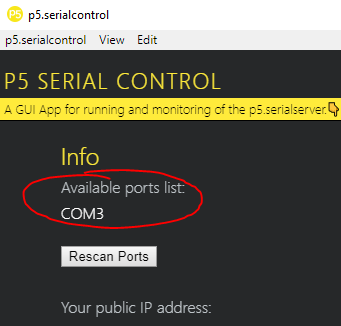
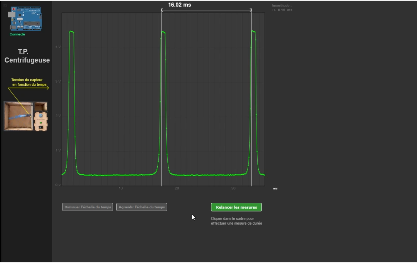
Pour accéder au T.P. , dirigez-vous sur cette page
2 – Programme autonome :
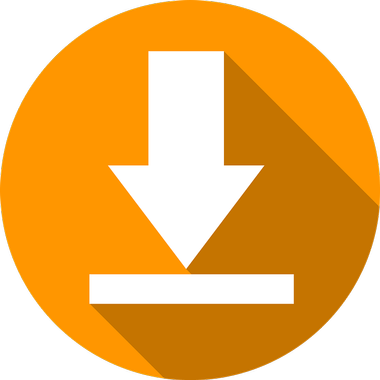
Le programme nécessite Java.
Si vous ne l’avez pas déjà installé.
Dézipper-le et lancer l’exécutable : centrifugeuse.exe
(la carte Arduino doit être programmée et branchée au préalable)